Compendium of 58 Most Useful KPIs for the Pulp & Paper Sector
- Dr. Marvilano
- Sep 1, 2023
- 3 min read
These KPIs are crucial for assessing the quality, efficiency, and sustainability of the paper manufacturing process.
1. Basis Weight Variation: The consistency or variation in the weight of paper produced, measured per unit area.
2. Biological Oxygen Demand (BOD) of Effluent: The amount of dissolved oxygen required by microorganisms to decompose organic material in effluent water.
3. Black Liquor Solids Production: The quantity of solid content produced during the black liquor recovery process.
4. Bleaching Efficiency: The effectiveness of the bleaching process in removing color from pulp.
5. Brightness Stability: The ability of paper to maintain its brightness over time and under various conditions.
6. Bursting Strength: The strength of paper to resist bursting under pressure.
7. Chemical Usage Efficiency: The efficiency of chemical usage in the paper manufacturing process.
8. CO2 Emissions per Ton of Production: The amount of carbon dioxide emitted per ton of paper production.
9. Creep (or Stretch) under Load: The degree to which paper stretches or deforms when subjected to a load.
10. Curl: The tendency of paper to curl, either towards the coated or uncoated side.
11. De-inking Efficiency: The effectiveness of the de-inking process in removing ink from recycled paper.
12. Effluent Treatment Efficiency: The efficiency of the treatment process in purifying wastewater before discharge.
13. Energy Self-Sufficiency: The extent to which the paper mill generates its own energy needs.
14. Fiber Efficiency: The efficiency in the utilization of fibers in the paper production process.
15. Fiber Sourcing Percentage: The proportion of fibers sourced from different materials in the paper-making process.
16. Filler Content: The proportion of filler materials used in the paper composition.
17. Fluff Pulp Production: The production volume of fluff pulp, often used in absorbent products.
18. Fold Endurance: The ability of paper to endure repeated folding without breaking.
19. Formation: The uniformity in the distribution of fibers and other components in the paper.
20. Internal Bond Strength: The strength of paper in resisting internal tearing.
21. Lignin Removal Efficiency: The effectiveness of the process in removing lignin from pulp.
22. Lime Mud Reburning Efficiency: The efficiency of lime mud reburning in the recovery process.
23. Lost Time Injury Frequency Rate (LTIFR): The frequency of lost time injuries per unit of work hours.
24. Moisture Content: The amount of moisture present in the paper.
25. Paper Break Frequency on Paper Machines: The frequency of paper breaks during the manufacturing process.
26. Paper Dusting: The release of dust or particles from the paper surface.
27. Paper Grade Change Frequency: The frequency of changing the grade or type of paper produced.
28. Paper Machine Efficiency: The overall efficiency of the paper-making machine.
29. Paper Smoothness: The smoothness or roughness of the paper surface.
30. Particulate Emissions: The release of particulate matter into the air during the paper production process.
31. Percent of Non-Wood Fiber: The percentage of non-wood fibers used in the paper composition.
32. Ply Bond Strength: The strength of the bonds between layers or plies in multi-ply paper.
33. Pulp Bleaching Sequences: The sequences or processes involved in bleaching pulp.
34. Pulp Consistency in Paper Machine Headbox: The consistency of pulp as it enters the paper machine headbox.
35. Pulp Detrimental Contaminants Level: The level of detrimental contaminants present in the pulp.
36. Pulp Dryness After Washing: The dryness achieved by pulp after the washing process.
37. Pulp Freeness: The degree of freedom of pulp fibers in water, affecting drainage.
38. Pulp Yield Percentage: The percentage of usable pulp obtained from raw materials.
39. Pulping Liquor Concentration: The concentration of chemicals in the pulping liquor.
40. Ratio of Coated to Uncoated Paper Production: The proportion of coated to uncoated paper produced.
41. Ratio of Mechanical to Chemical Pulp: The ratio of mechanically produced pulp to chemically produced pulp.
42. Ratio of Softwood to Hardwood Pulp: The ratio of softwood fibers to hardwood fibers in the pulp composition.
43. Recycled Fiber Usage: The proportion of recycled fibers used in paper production.
44. Retained Ash Content: The amount of ash content retained in paper after combustion.
45. Stiffness: The stiffness or rigidity of the paper.
46. Sulfur Emissions: The release of sulfur compounds into the air during the paper production process.
47. Tear Resistance: The resistance of paper to tearing.
48. Tensile Strength: The maximum tensile stress a material can withstand.
49. Thermal Conductivity of Paper: The ability of paper to conduct heat.
50. Total Reduced Sulfur (TRS) Emissions: The release of total reduced sulfur compounds during the paper production process.
51. Volatile Organic Compounds (VOC) Emissions: The release of volatile organic compounds into the air.
52. Waste Paper Recovery Rate: The percentage of waste paper that is recovered and recycled.
53. Water Use per Ton of Product: The amount of water used per ton of paper produced.
54. Whiteness: The brightness or whiteness of the paper.
55. Wood Chip Hardness: The hardness of wood chips used in the paper production process.
56. Wood Chip Size Consistency: The consistency in size of wood chips used in the paper-making process.
57. Wood Chip Yield: The yield or efficiency in obtaining usable material from wood chips.
58. Wood Usage Efficiency: The efficiency in the utilization of wood in the paper production process.
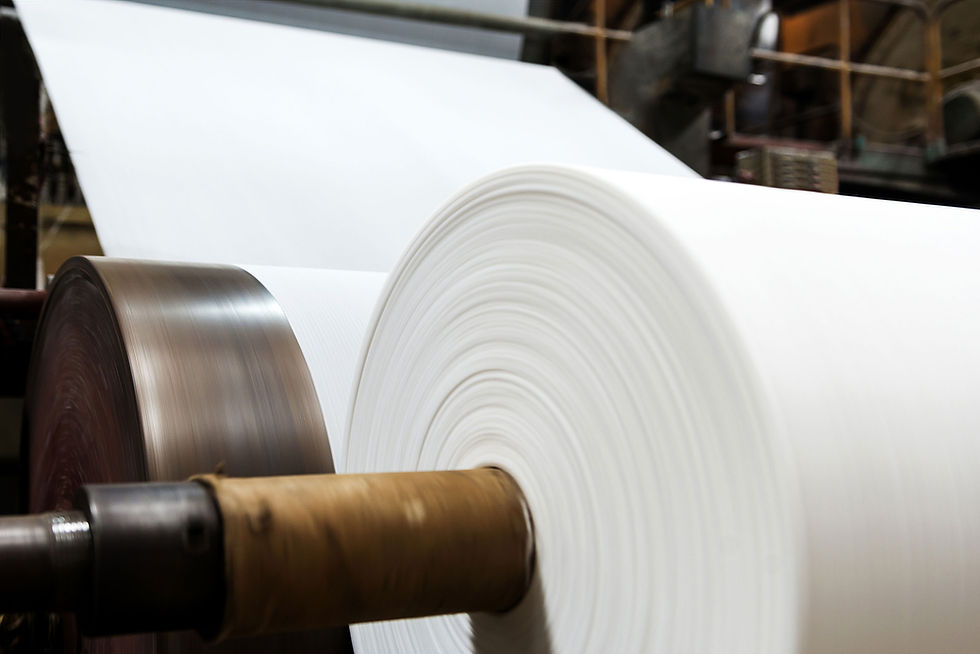
Comments